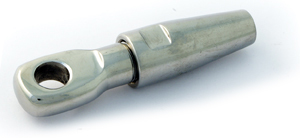
This product highlight contains safety-critical technical information regarding how the number of slots in the cone of a swageless fitting effects holding power. We make important recommendations for the safe design of swageless compression terminals based on extensive testing - please read.
The Hi-MOD swageless compression terminals were first developed by Petersen Stainless Rigging Ltd after a request from a manufacturer of roller-furling gear. The existing systems in the market required the bending of the wires inside the terminal. The brief was to develop a swageless terminal which would not damage the wire end so that a furler could be removed from the headstay without having to cut off the end of the wire.
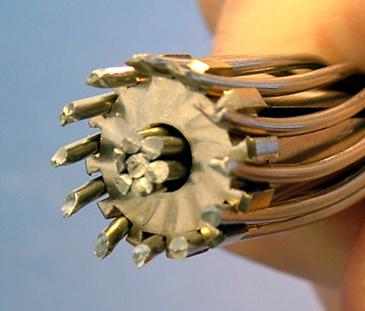
During the design process tests were carried out to establish the effectiveness of a 'single-slot' cone design as we found to be common in the market. The graphs below show the comparative performance of 3mm 1x19 fittings with one and two slots in the cone. The difference in the results is quite staggering. While a two-slot cone is able to close easily onto the rope core and spread the load evenly between all the wires a single-slot cone needs a much larger force to do so. The clamping force comes from the tension in the wire and so a large load must be applied to the outer wires before a single-slot cone can grip the core. The effect of this principle was easily seen when examining the test pieces afterwards. The cores pulled a long way through the cone before finally being gripped and as can be seen by the large variability in the failure loads the amount the core pulled through was by no means consistent. Consequently all Petersen Hi-MOD swageless compression fittings have a minimum of two slots in the cones - some of the largest have six.
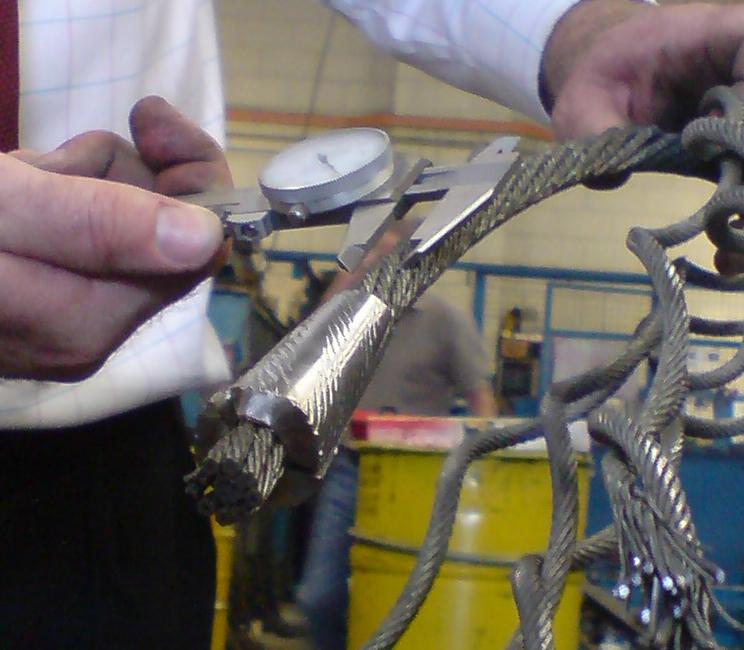
Petersen also took the opportunity to address some of the other common shortcomings they saw in the products already on offer. The crown-ring (originally only intended as a spacer) was notched to ensure an even distribution of the wires inside the fitting even after tightening. The cone angle was reduced to give better grip on compacted strands such as Dyform. The end-fittings were recessed so that protruding wire ends would not interfere with the threads to reduce the likelihood of galling. Finally the decision was made to use high-grade materials throughout so that the fitting wouldn't need to be filled with sealant on assembly.
The recommendation not to use sealant is very important. Wire-ropes are porous and sealant can not prevent water from getting inside fittings. Stainless steel relies on a ready supply of oxygen to renew its corrosion resistance - provided by a thin film of chrome-oxide on the surface. Water usually contains plenty of dissolved oxygen to allow the chrome-oxide layer to constantly replenish however stale water (such as can be found inside a badly sealed fitting) does not contain enough dissolved oxygen to allow this to take place and consequently is very corrosive to stainless steels. By choosing high grade bronze and 316L for the Hi-MOD swageless compression fittings we were able to do away with the need for sealant and allow air and fresh water to get inside and keep up the supply of oxygen.
The last innovation was to tailor the design to allow for easy assembly using the 'twist-click' method. Holding the end-fitting against the crown ring you simply have to twist the body with the lay of the wire while applying upward pressure. The outer wires will then simply 'click' into place. Some may get crossed in the process but this is easily remedied in a matter of seconds with the point of a screwdriver. This method of assembly is extremely quick and easy to do even on large diameter and compacted strands - something that will be appreciated by anyone who has ever had to bend a large wire end into a fitting! We used to have a video of a fitting being assembled onto a 16mm 1x19 strand in under 40 seconds from a cut and closed end but we thought people would think it was a trick so we never showed it to anyone.
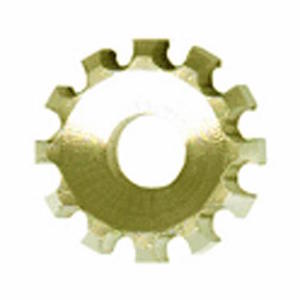
In summary the key features of the Petersen Hi-MOD swageless compression terminals are:
- Ideal for use with headstay furlers
- Cones have a minimum of two slots for better grip of core
- A gentle taper on the cone gives better grip of Dyform / Compact Strand
- The crown ring prevents wires getting stuck in the cone slots
- The slots in the crown ring give positive confirmation of correct assembly
- Recessed end-fittings to prevent thread damage from wire ends
- Wire end do not require bending
- No sealant or filler required
- Very quick to assemble resulting in increased productivity

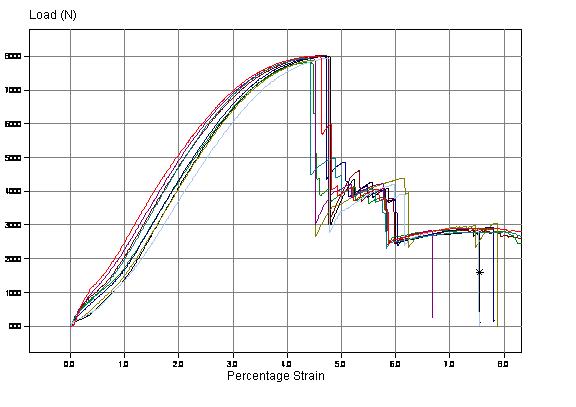
It is clear that the two-slot cone is a stronger and more consistently performing design.